やはり凄い技術なんだなぁー!
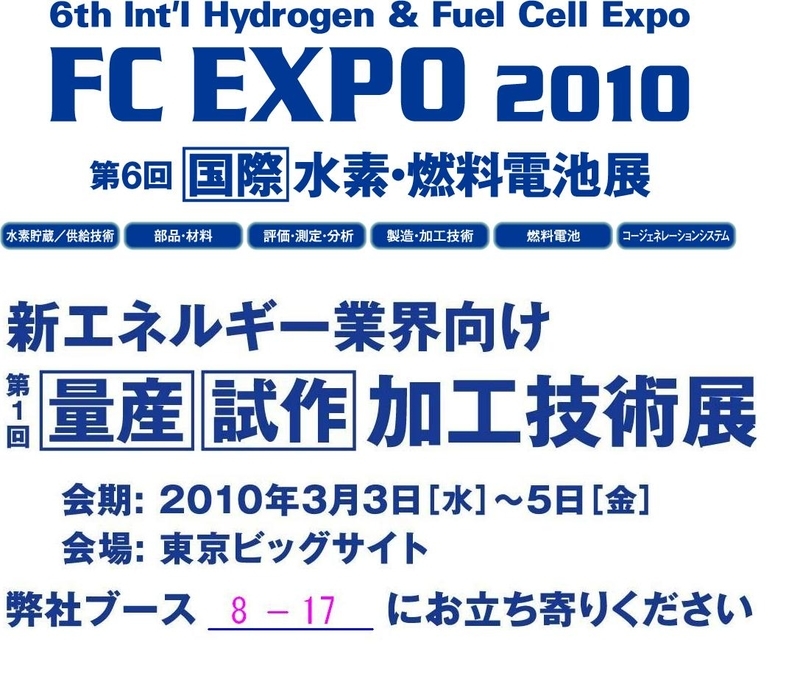
”Magic Restriking"
今回の展示会に出展する技術を改めて考えた時、本当に凄い技術だと感心する。
燃料電池のセパレータには必ず流路が必要なのだが、当初、カーボンの射出成形など、素材を金型で圧縮して流路を確保する方法が取られていて、繰り返し、試作テストが行われて来た。
しかし、実用化に向けてコストダウンが迫られ、最近この10年近く、金属製セパレータに注目が集まったようで、材料メーカーのS社やD社、更にはH社などが、金属セパレータ用の専用材を開発し、また、量産技術なども研究開発され、S社の研究員は「量産性や品質を悩ませてきた問題点は、ほぼ解消された。」と言っている。
しかし、私も金属プレス金型業界で直接・間接的に34年も携わってきて、どれだけ優秀な凄い新技術を駆使して作った物なのか、ネット上に紹介されている、問題点が解消されたと言う金属製セパレータを見たが、その流路は、通常の成形ビードを上げ下げした物で、金型業界では極単純な、今まで長い間ずーっと使われてきた技術だった。
燃料電池の性能云々は、私にはよく分からない。あくまで私見であるが、幾重にも積層して作る燃料電池スタックを見る限り、ビードの山と山で壁を作っていたり、積層時に板厚の隙間を埋める部品の必要性や、厚みが厚くなる分、抵抗値が増加するように見えて仕方がない。
その点、当方で紹介させて頂く流路確保技術は、板厚0.2ミリの中に、板厚を変えずに、溝巾はスタックメーカーのデザインで任意、溝深さは0.15MAXで、それも、プレスで加工する物だ。
更には、裏表交互に流路を確保出来ると言うのだ。
つまり、板厚0・2の裏表に流路が形成された金属製のセパレータがプレス加工で量産出来ると言うのだ。
しかし、プレス業界関係者の方なら誰でも分かる常識だが、通常、プレス加工で叩いて凹ませたら、応力でぐちゃぐちゃに反り返ってしまい、積層出来る形状ではなくなってしまう。とても製品として成り立たない。
ここで、”Magic Restriking"の出番だ!!
上記の反り返ったり、部分的に膨らんだり凹んだりした薄板を、0.02以下の平面度に、一発でピタッと平らにしてしまうのだ。
しかも、一切、ベコベコしない。とても信じられない。まさに魔法だ!!
燃料電池スタックメーカーの皆様。
1スタックのセパレータの厚みが、両側で最小0.4ミリになります。
プレスにて量産可能ですので、セパレータのコストダウン、抵抗値減少による性能アップ、H社専用材料による諸問題の世界最高峰レベルでの回避。
燃料電池の実用化は、すぐそこにやって来ています。
展示会当日、当方ブースにてご確認下さい。